A Comquality é uma empresa pioneira e inovadora no entrega de soluções em atmosferas explosivas e hoje iremos abordar nosso processo de inspeção Ex.
Potentially Explosive Atmospheres and Classified Areas
Potentially explosive atmospheres and classified areas are directly related to the presence of flammable substances in concentrations sufficient to pose a significant risk of explosion or fire upon contact with an ignition source. These areas are common in various industries, such as petrochemical, chemical, pharmaceutical, food, energy, and others.
Inspection Core in Explosive Atmospheres
Electrical installations in classified areas require special attention, as the presence of flammable gases and combustible dust can cause explosions. The inspection core in classified areas works to verify and evaluate the integrity, functionality, and suitability of equipment and installations in compliance with regulatory requirements.
Types of Inspections We Provide
Visual Inspection:
Identifies visually perceptible defects, such as missing screws and broken enclosures.
Thorough Inspection:
Includes visual aspects along with the use of tools to identify defects not visible to the naked eye.
Detailed Inspection:
Incorporates aspects of both Visual and Thorough inspections, along with the identification of possible internal enclosure faults.
Comquality Innovation
Comquality is a pioneering and innovative company in providing solutions for explosive atmospheres. It has distinguished itself through an innovative approach to using computerized systems for conducting Ex inspections offline. This approach utilizes Ex tablets and smartphones to perform inspections in hazardous environments.
Thanks to this groundbreaking technological solution, Comquality has been able to optimize the inspection, monitoring, and reporting process for one of the largest companies in Brazil, making them more efficient and secure.
Inspection Reports are generated in real-time, directly in the field, and automatically synchronized with Comquality’s central system. This process allows for immediate communication between the inspection team and the team responsible for analyzing client company reports.
Inspection Stages
Comquality has a specialized process for inspecting and maintaining equipment and installations in explosive atmospheres, which is divided into the following stages:
Initial Analysis and Inspection Planning
Before starting the inspection in explosive atmospheres, it is crucial to conduct an initial analysis of the area to be inspected. This involves identifying classified areas, which are locations where the presence of explosive atmospheres is likely, and determining the types of risks present. Based on this information, inspection planning is done, including defining the necessary equipment and tools, assigning the inspection team, and creating a schedule.
Equipment Identification
During the inspection, the responsible team identifies and evaluates all equipment present in the classified area. This includes instruments, machinery, electrical devices, and any other equipment that may pose risks in explosive atmospheres. The team checks whether these devices are properly certified for use in hazardous areas and comply with applicable safety standards.
Identification of Non-Conformities
In this stage, the team looks for any non-conformities or faults in equipment and installations. Items such as seals, leaks, wear and tear, corrosion, dust or residue accumulation, and other issues that may pose ignition or explosion risks are examined. All identified non-conformities are documented for subsequent correction.
Inspection Report
Throughout the inspection, the team compiles a detailed report with all relevant information collected. This report includes findings of non-conformities, descriptions of inspected equipment, verified classified areas, and any other important observations. This document is crucial for documenting the activities performed and certifying the safety of the area to regulatory authorities and stakeholders.
Correction of Installations
Based on the non-conformities identified in the inspection report, corrective actions are taken to eliminate or mitigate the identified risks. This may include replacing damaged equipment, performing repairs, adjustments, or even making modifications to installations to ensure compliance with safety standards.
Conducting a New Inspection
After correcting the non-conformities, a new inspection is conducted to verify the effectiveness of corrective measures and to ensure that the area now complies with safety standards. This step is essential to ensure that there are no longer risks of explosions or other hazards.
Final Inspection Report
Following the correction of installations and a new inspection, a final report is prepared, attesting that all non-conformities have been addressed and that the inspected area complies with explosive atmospheres regulations. This report is important for documenting the activities performed, as well as certifying the safety of the area to relevant authorities and stakeholders.
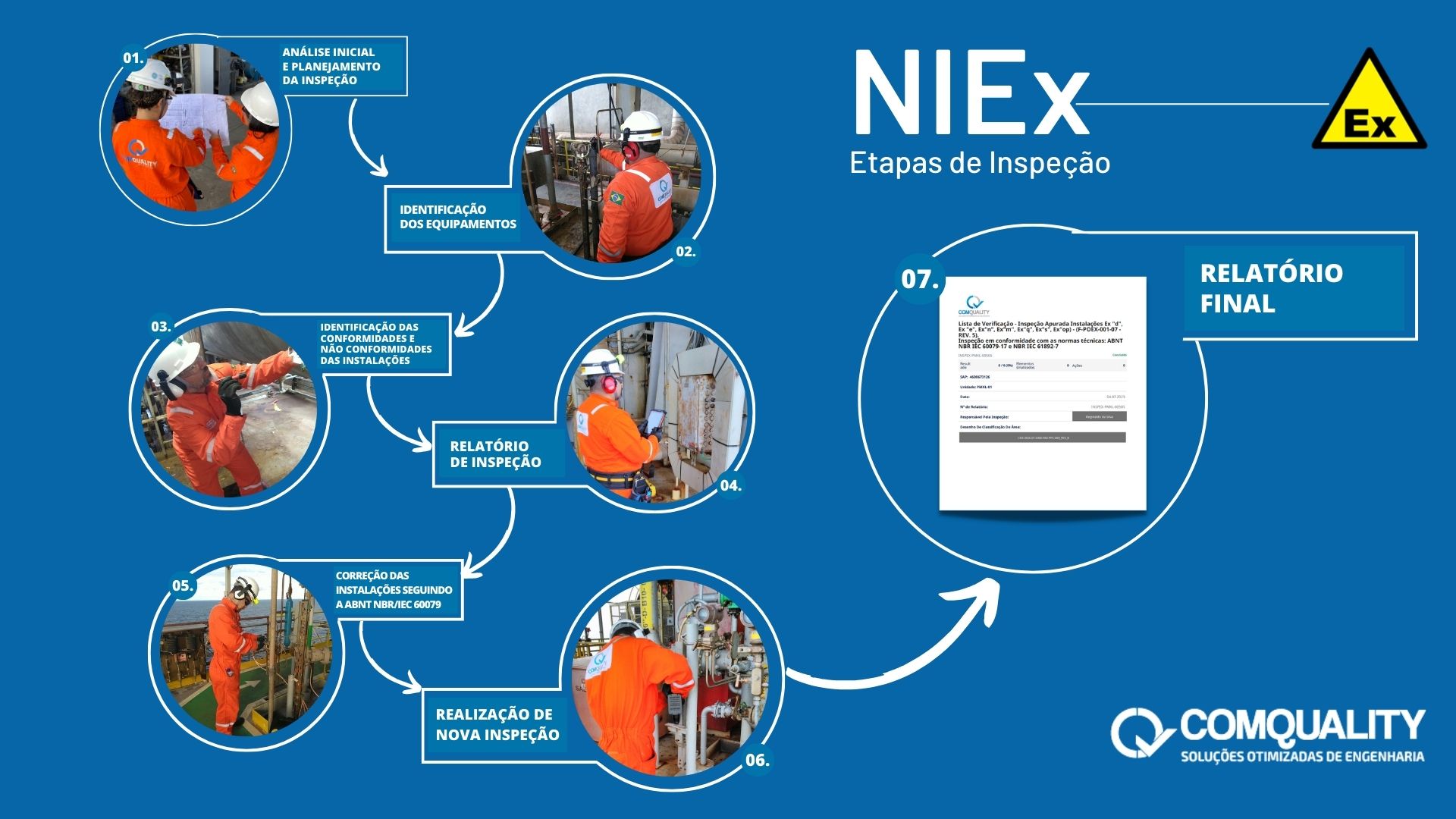
Comquality Specializes in Delivering Solutions for Explosive Atmospheres
We have a highly qualified team of experts who hold Ex personal competency certification for work in classified areas. Furthermore, we are the third company in Brazil to be certified under ABNT NBR IEC 60079-17 standard.
We specialize in delivering solutions for explosive atmospheres. Please contact our team now to ensure the safety of your company’s equipment and installations in potentially explosive environments!
📞 71 3622-1255
📩 comercial@comquality.com.br
🌎 www.comquality.com.br
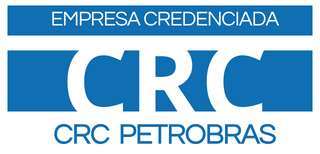